Диссольверы (промышленные миксеры)
Диссольверы (или промышленные миксеры) – это оборудование для смешивания и измельчения частиц твердого или жидкого материала, в жидких и пастообразных средах под воздействием вращения дискофрезной мешалки.
Диссольверы применяют для производства керамических шликеров на водной основе, эмалей лаков, красок, клеев и различных покрытий, ПВХ паст.
Чаще всего диссольверы используют для измельчения и равномерного распределения порошкообразных частиц в жидкости. Диссольверы могут применяться для смешивания жидкостей или паст с разной консистенцией, а также для диспергации, эмульгации, дезагрегации порошков в жидких средах и приготовления многокомпонентных составов.
Отрасль применения |
|
|
|
|
|
|
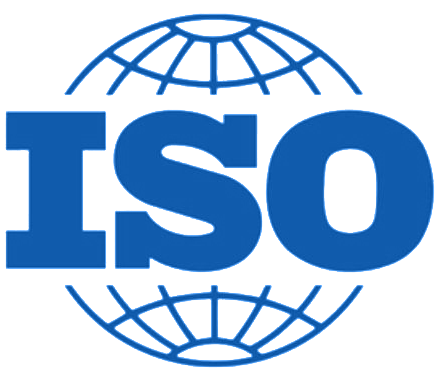
Система менеджмента качества сертифицирована (ISO 9001:2008)
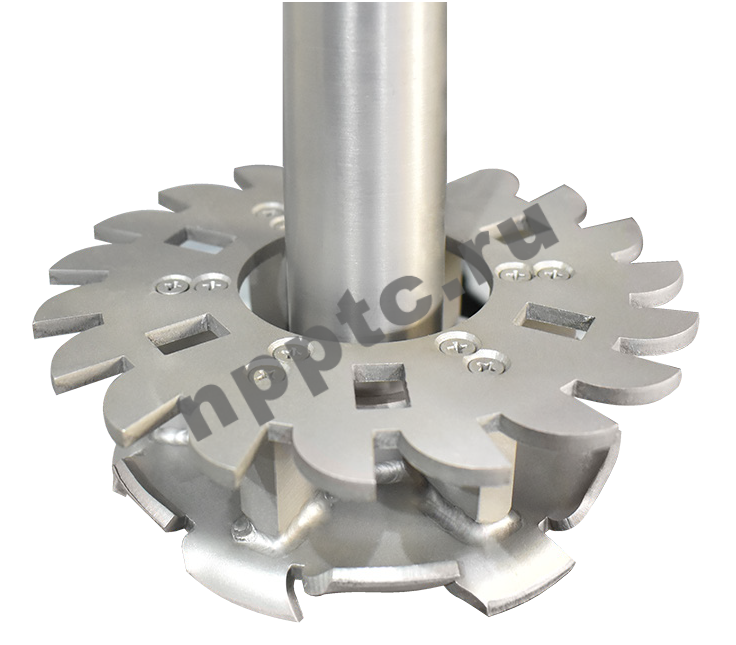

Основные технические характеристики лабораторных диссольверов,
а также для малых и средних производств.
Модель |
СДИ-1 |
СДИ-3 |
СДИ-5 |
СДИ-10 |
СДИ-30 |
СДИ-60 |
Общий объем емкости, л |
1 |
3 |
5 |
10 |
30 |
60 |
Рабочий объем ёмкости, л * |
0,3-0,7 |
0,9-2,1 |
1,5-3,5 |
3-7 |
9-21 |
18-42 |
Максимальная частота оборотов емкости, об/мин |
7000 |
7000 |
3000 |
3000 |
3000 |
3000 |
Установленная мощность, не более, кВт ** |
1 |
1,5 |
2,2 |
3 |
5,5 |
7,5 |
Габаритные размеры (ДxШxВ), не менее, мм *** |
600 |
760 |
760 |
760 |
1400 |
1600 |
Масса, не более, кг *** |
85 |
140 |
160 |
250 |
650 |
1000 |
Технические характеристики смесителей |
Серии СДИ |
|||||
Основное применение |
Смешивания жидкостей или паст, диспергация, эмульгация, дезагрегация порошков в жидких средах, приготовление различных составов. |
|||||
Тип смешивания * |
Суспензии и текучие среды различной вязкости |
|||||
Материал смесительной ёмкости и мешалок |
Нержавеющая сталь |
|||||
Загрузочный коэффициент * |
0,3-0,7 от общего объема |
|||||
Количество мешалок |
1 |
|||||
Типы устанавливаемых мешалок |
Дисковая фреза, многоярусные фрезы. |
|||||
Конструктивные исполнения |
Без подъема-опускания мешалок/емкости С механизмом подъема-опускания ёмкости С механизмом подъема-опускания мешалок |
|||||
Выгрузка готового состава |
через затвор в нижней части емкости / поворотом смесительной ёмкости. |
|||||
Нагрев смесительной емоксти |
Рубашка для подачи жидкого теплоносителя / электронагрев (опция) |
|||||
Система вакуумирования рабочей камеры |
остаточное давление до -0,9 атм (опция) |
|||||
Регулировки частоты оборотов |
Частотным преобразователем (опция) |
|||||
Задание времени работы |
Таймером (опция) |
|||||
Подключение к сети электропитания |
220В, 50Гц / 380В, 50Гц |
* Данные параметры зависят от физико-механических свойств смешиваемого материала и определяются опытным путем при обработке технологии на каждом отдельном виде материала.
** Мощность смесителя зависит от максимальной частоты оборотов мешалки, вязкости смешиваемых составов, максимальной температуры нагрева смесительной емкости (дежи) и конструктивного исполнения смесителя (с подъемом / без подъема) – параметры подбираются индивидуально.
*** Габаритные размеры и масса смесителей определяются конструктивным исполнением и объем смесительной ёмкости.
Основные технические характеристики промышленных диссольверов:
Модель |
СДИ-100 |
СДИ-150 |
СДИ-300 |
СДИ-500 |
СДИ-1000 |
СДИ-2000 |
Общий объем емкости, л |
100 |
150 |
300 |
500 |
1000 |
2000 |
Рабочий объем ёмкости, л * |
30-70 |
45-105 |
90-210 |
150-350 |
300-700 |
600-1400 |
Максимальная частота оборотов мешалки, об/мин |
3000 |
3000 |
1500 |
1500 |
1500 |
1500 |
Установленная мощность, не более, кВт ** |
11 |
11 |
15 |
18 |
22 |
30 |
Габаритные размеры (ДxШxВ), не менее, мм *** |
1600 |
1650 |
1800 |
2000 |
2600 |
3200 |
Масса, не более, кг *** |
1200 |
1400 |
1800 |
2100 |
3300 |
4800 |
Технические характеристики смесителей |
Серии СДИ |
|||||
Основное применение |
Смешивание и приготовление маловязких и вязких паст, взмучивания осадков. |
|||||
Тип смешивания * |
Суспензии и текучие среды различной вязкости |
|||||
Материал смесительной ёмкости и мешалок |
Нержавеющая сталь |
|||||
Загрузочный коэффициент * |
0,3-0,7 от общего объема |
|||||
Количество мешалок |
1 |
|||||
Типы устанавливаемых мешалок |
Дисковая фреза, многоярусные фрезы. |
|||||
Конструктивные исполнения |
Без подъема-опускания мешалок/емкости С механизмом подъема-опускания мешалок |
|||||
Выгрузка готового состава |
через затвор в нижней части емкости |
|||||
Нагрев смесительной емоксти |
Рубашка для подачи жидкого теплоносителя / электронагрев (опция) |
|||||
Система вакуумирования рабочей камеры |
остаточное давление до -0,9 атм (опция) |
|||||
Регулировки частоты оборотов |
Частотным преобразователем (опция) |
|||||
Задание времени работы |
Таймером (опция) |
|||||
Подключение к сети электропитания |
220В, 50Гц / 380В, 50Гц |
* Данные параметры зависят от физико-механических свойств смешиваемого материала и определяются опытным путем при обработке технологии на каждом отдельном виде материала.
** Мощность смесителя зависит от максимальной частоты оборотов мешалки, вязкости смешиваемых составов, максимальной температуры нагрева смесительной емкости (дежи) и конструктивного исполнения смесителя (с подъемом / без подъема) – параметры подбираются индивидуально.
*** Габаритные размеры и масса смесителей определяются конструктивным исполнением и объем смесительной ёмкости.
Дополнительная комплектация и модернизация:
- Изготовление мешалок различных форм по заданию Заказчика.
- Изготовление дополнительных сменных мешалок различной формы для каждого смешиваемого состава (например: мешалка бабочка для вязких паст + дискофрезная мешалка для диспергирования порошков в жидких средах).
-
Оснащение высокоскоростной дисковой фрезой меньшего или большего размера, несколькими ярусами высокоскоростных фрез на валу.
- Увеличение частоты оборотов дискофрезной мешалки по заданию Заказчика.
- Нанесение защитных твердосплавных покрытий на зубцы высокоскоростной дисковой фрезы для уменьшения износа при диспергировании абразивных материалов.
- Оснащение смесителя системой вакуумирования.
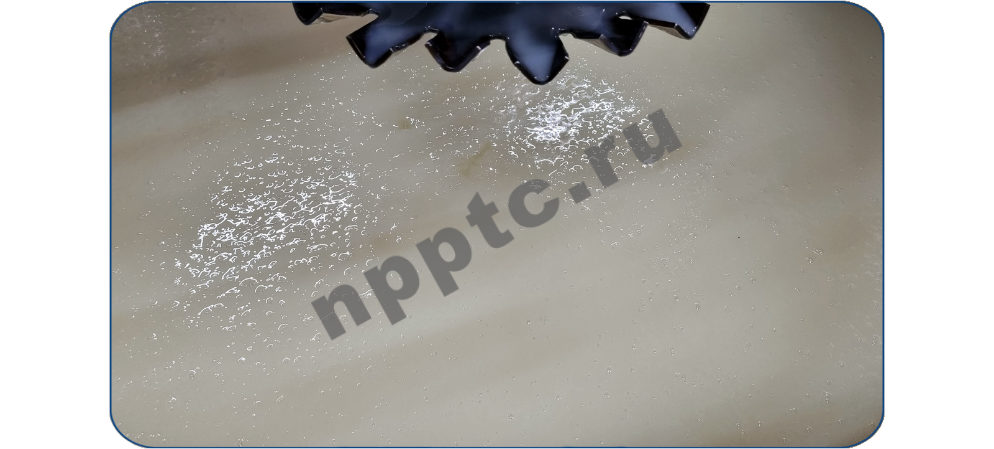
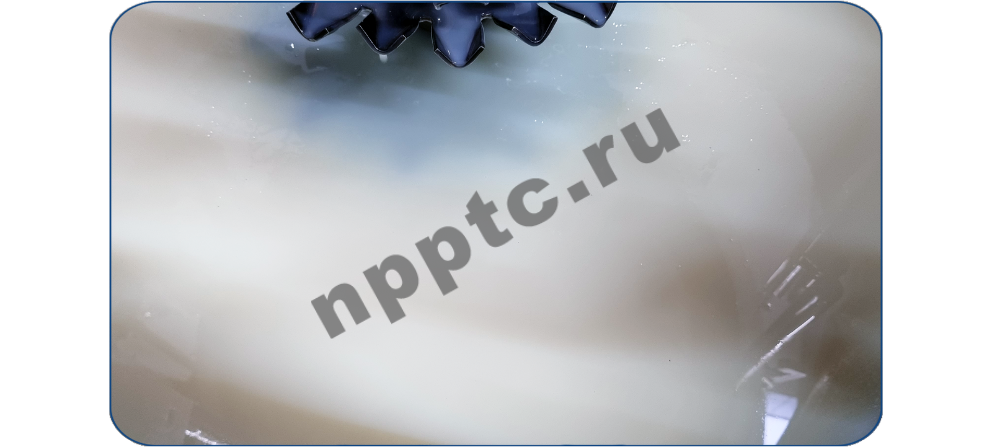
- Исполнение с возможностью подключения к системе вакуумирования.
- Оснащение системой для подачи в рабочую камеру инертного газа (азот, аргон).
- Изготовление электрической части во взрывобезопасном исполнении.
- Регулировка частоты оборотов электродвигателя.
- Задание времени смешивания таймером.
- Оснащение смесителя системой автоматического снижения скорости при повышении/снижении вязкости или температуры смешиваемых составов.
- Комплектация смесителей агрегатом для нагрева и подачи жидкого теплоносителя в рубашку смесительной емкости.
- Оснащение смесителей встроенной системой электронагрева смесительной емкости (ТЭНами).
- Система охлаждения смесительной емкости с помощью чиллера.
- Установка термопар для измерения температуры.
- Оснащение смесителя встроенным пирометром для дистанционного измерения температуры смеси.
- Дополнительные дежи различного объема и конфигурации по заданию Заказчика:
- Изготовление смесительных емкостей из разных материалов.
- Изготовление смесителей по техническому заданию Заказчика.
- Покрытие внутренней поверхности смесительной емкости, крышки и мешалок различными материалами.
- Исполнение смесителя открытого типа для смешивания материалов в универсальных пластиковых бочках объемом от 48 до 227 или металлических бочках объемом от 100 до 200 литров.
- Исполнение смесителя с универсальным креплением деж разного диаметра (тросом с натяжителем).
- Изменение расстояния между высокоскоростной фрезой и дном дежи.
- Оснащение системой замывки смесительных емкостей от трудно очищаемых продуктов.
- Изготовление бисерной насадки на высокоскоростной вал смесителя.
- Оснащение смесителя специализированным нагревателем для бочек или шкафом для нагрева.
- Оснащение смесителя грузоподъемным механизмом с оснасткой для фиксации и поворота бочек.
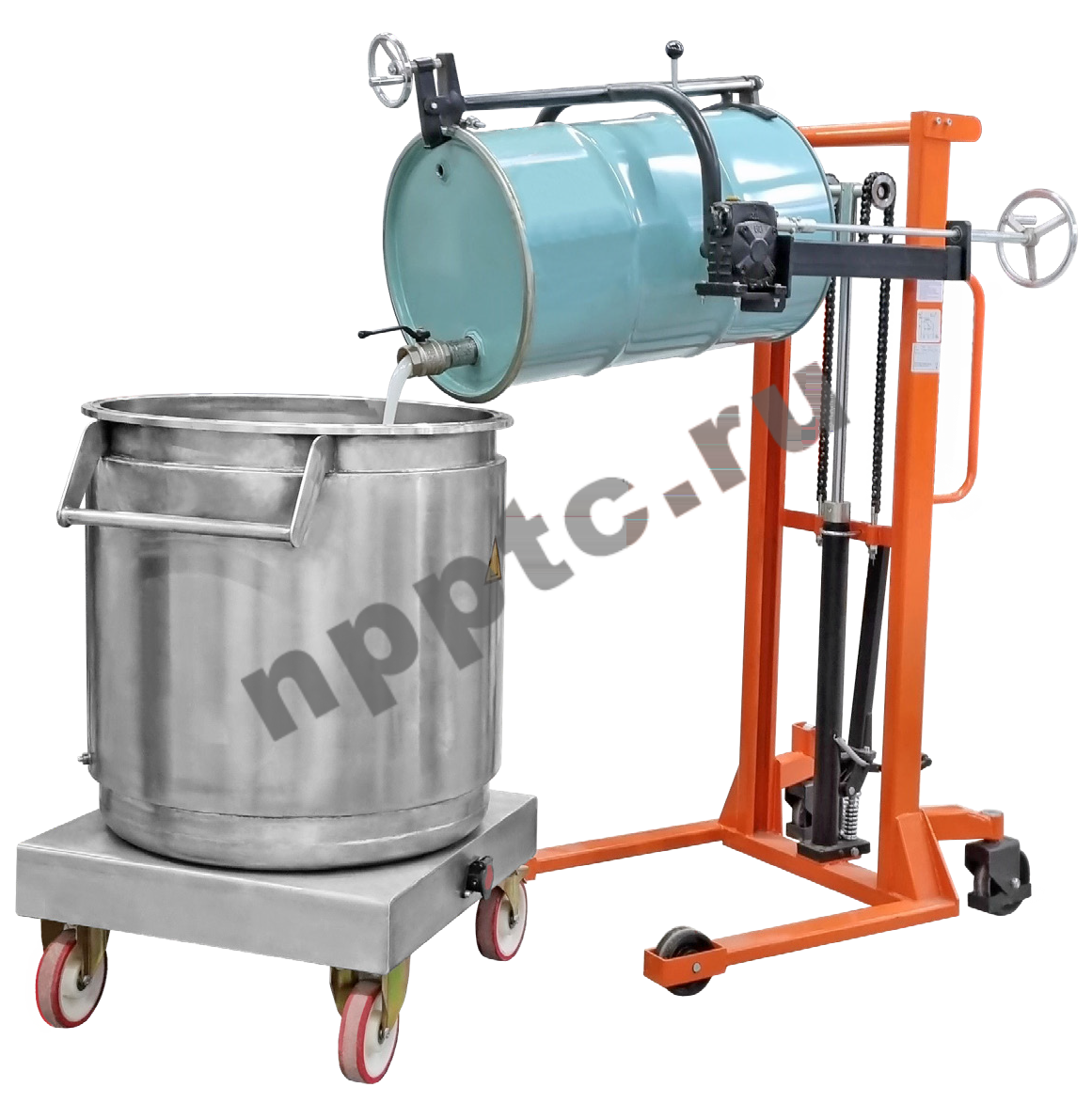
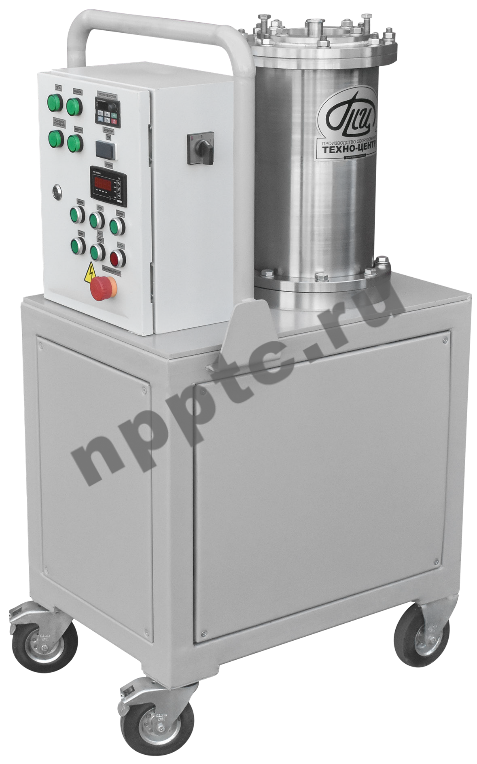
- Оснащение смесителя дозатором для паст
- Комплектация платформенными весами для измерения веса дежи при загрузке компонентов смеси.
- Оснащение смесителя пресс-экструдером для обеспечения выгрузки материала высокой вязкости.
- Оснащение смесителя подъемным устройством для выгрузки материала из дежи на необходимой высоте.
- Комплектация воронкой для загрузки порошка в дежу.
- Установка смотровых стекол с подсветкой.
- Оснащение смесителя питателем для сухих порошков (вибропитатель / шнековый питатель).
- Существует возможность проведения предварительных испытаний на лабораторном смесителе с материалом Заказчика на территории нашего завода.
- Благодаря подобранным параметрам конфигурации мешалок и смесительной емкости, обеспечивается интенсивное смешивание, сдвиг и сжатие, а также разнонаправленное движение смеси по всему объему перемешиваемого состава, что обеспечивает высокое качество готового материала.
- Кинематика работы смесителей обеспечивает полноценное смешивание всего объема состава (отсутствие застойных зон).
- Конструкция перемешивающих органов обеспечивает эффективное смесеприготовление различных составов за минимальный временной промежуток.
- При работе смесителей обеспечивается циркуляция составов внутри смесительной емкости, это повышает равномерность и однородность готового состава.
- Высокая производительность и эффективность процесса диспергирования и перемешивания.
- Конструкция смесителей обеспечивает удобный доступ к перемешивающим органам для выполнения замывки смесительной емкости смешивающего элемента:
- Подъем и опускание рабочей емкости / мешалок, выполняется автоматическим или ручным лифтовым механизмом – обеспечивает быстрый и удобный доступ к рабочим органам.
- В опущенном состоянии рабочая емкость большинства лабораторных смесителей имеет возможность поворота на 90 градусов по горизонтальной (относительно центра мешалки).
- Встроенная рубашка для охлаждения смесительной емкости.
- Механизация подъема-опускания емкости обеспечивает возможность эксплуатации женским персоналом - работа не требует значительных физических усилий.
- В крышке смесителя встроены смотровые стекла для наблюдения и контроля процесса перемешивания.
- Смесители оснащены необходимыми блокировками и безопасны для оператора, а удачность конструкции обеспечивает простоту в работе и обслуживании.
- Смесительная емкость выполнена из нержавеющей стали 12Х18Н10Т – данная сталь не подвержена коррозии (также при дезинфицировании емкости с моющими добавками).
- Уплотнения для герметизации смесителей устойчивы к агрессивным средам, имеют высокую маслостойкость и износостойкость.
- Дежа с рубашкой для подачи теплоносителя позволяет выполнять обогрев или охлаждение смешиваемого состава.
- Конструкция обеспечивает удобный доступ к перемешивающим органом для выполнения замывки.
- Для продуктов с высокой вязкостью скребок для стенок и дна дежи может облегчить процесс смешивания и диспергирования, а также очистку смесительной емкости.
- Ввод компонентов в процессе смешивания выполняется через загрузочный лючок в крышке дежи.
- Быстросъемные дежи (смесители до 10 л) и выкатные дежи (смесители от 30 до 2000 л) позволяют выполнять транспортировку готовой смеси в зону технологического применения.
- Устройства-захваты (смесители от 30 до 2000 л) позволяют быстро и точно позиционировать выкатную дежу большого объема относительно перемешивающих органов.
- В конструкции смесителей применяются надежные серийные подшипники с высоким ресурсом работы.
- Малогабаритность, компактность, малый вес, отсутствие необходимости пусконаладочных работ («подключил и работай»).
- Технологичность конструкции и запас прочности обеспечивают многолетнюю эксплуатацию смесителей без выполнения ремонтных операций.
- Система управления обеспечивает удобство в обслуживании и в работе (в том числе при отработке новых технологических режимов работы):
- Система ПИД регулирования температуры позволяет автоматически поддерживать заданную температуру смешиваемого состава с высокой точностью, а также настраивать оптимальную мощность и интенсивность нагрева в зависимости смешиваемого материала (опция);
- Возможность автоматического снижения частоты фрезерной мешалки при повышении температуры смеси;
- Регулировка частоты оборотов позволяет оператору в широком диапазоне плавно изменять интенсивность смешивания (опция).
- Время смешивания задается таймером.
Для диспергации в диссольвере обычно требуется предварительный этап смешивания, во время которого всю необходимую массу порошка постепенно тонкой струей ссыпают в жидкость с постепенным ускорением вращения фрезы от медленной до образования воронки в форме «бублика». Если во время этого процесса смесь налипла на вал диссольвера, то следующим этапом будет чистка диска фрезы и стенок рабочей емкости от налипшей массы. После этого приступают непосредственно к самому процессу диспергирования.
Во время процесса диспергирования необходимо увеличить окружную скорость диска диссольвера до 20 м/с (от 18 до 25 м/с). Смесь при такой скорости образует воронку, на дне которой видно верхнюю часть диска фрезы. Форма такого потока жидкости похожа на «бублик» (изображено на рисунке). На схеме под цифрами показаны 1 - емкость, 2 – смесь в движении в форме бублика, 3 - направления движения смеси, 4 - дисковая фреза.
Смесь радиально ускоряется дисперсионным диском, отклоняется вверх и вниз у стенки рабочей емкости и затем снова направляется к дисперсионному диску за счет образования вихревых потоков. В процессе диспергирования постепенно твердые частицы разделяются на более мелкие и равномерно распределяются в смеси. Обычно качественное диспергирование достигается уже через 10-15 минут. С помощью специальных добавок можно ускорить процесс диспергирования и предотвратить слипание твердых частиц в смеси (флокуляцию).
Процесс диспергации происходит на краю фрезерного высокоскоростного диска, поэтому окружную скорость следует рассматривать как основной параметр для масштабирования лабораторных результатов.
Диссольверы (или промышленные миксеры) – это оборудование для смешивания и измельчения частиц твердого или жидкого материала, в жидких и пастообразных средах под воздействием вращения дискофрезной мешалки.
Диссольверы применяют для производства керамических шликеров на водной основе, эмалей лаков, красок, клеев и различных покрытий, ПВХ паст.
Чаще всего диссольверы используют для измельчения и равномерного распределения порошкообразных частиц в жидкости. Диссольверы могут применяться для смешивания жидкостей или паст с разной консистенцией, а также для диспергации, эмульгации, дезагрегации порошков в жидких средах и приготовления многокомпонентных составов.
Свяжитесь с нами удобным способом
пн-пт с 8:00 до 17:00, обед с 12:00 до 13:00
г. Рыбинск, ул. Нансена, д.20 Схема проезда
Рысев Владимир Александрович
8 (800) 100-77-23 (Технический отдел)
Оставьте свои данные и наш менеджер свяжется с вами в ближайшее время
мы получили вашу заявку
Наш специалист свяжется с вами в ближайшее время, для уточнения необходимой информации